Steps to climate proof your brewery
To make beer, you need a lot of water. And you need good water. The availability and quality of the water will increasingly dictate where beer will be produced. These are all well-known facts.
DATE 2025-01-13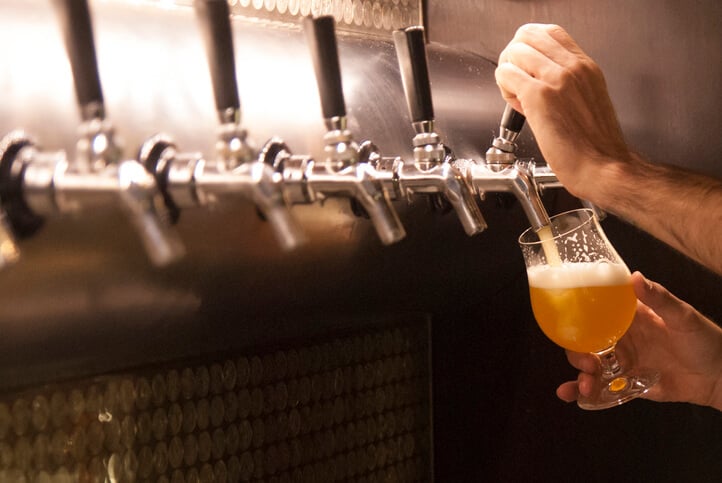
Now, the adaptation to climate changes and their effect on the availability of water have become mainstream in the brewery industry. “Breweries are increasingly looking at climate proofing their plants – incorporating the risks of climate change into their mitigation and adaptation plans,” says Maria Lindmark, Head of Revos at Alfa Laval. “And they are also acutely aware that sustainable production will speak to increasingly climate-conscious consumers.”
Thanks to her interaction with a large group of breweries from around the world, it is apparent to her that the impact of climate change is sharpening the focus on water usage and its uninterrupted supply. “Water security is a showstopper when breweries are considering where to place their next plant,” she says.
In places where water stress has long been par for the course – such as Mexico, sub-Saharan Africa and the southwestern part of the USA – breweries already know the drill. They have plans in place to continuously optimize the water consumed per hectolitre of beer produced.
“All breweries have different water targets depending on whether they operate in a geography with water stress or not. Now, we are seeing breweries completely disregarding a location during the planning for a new plant and looking somewhere else if they are not convinced of future water security in the first location. Producing beer close to a megacity is becoming very difficult because most of them already struggle with the availability and treatment of water,” says Maria.
Existing breweries
Meanwhile, existing breweries will have to search for an alternative solution. One way is to upgrade legacy sites with outdated technologies, so they operate with a much higher efficiency and yield – an expensive and time-consuming approach. Another way is to make existing sites to operate differently. “A circular water system can enable sustainable production of beer and other water-laden beverages such as soft drinks in a location with water stress. By optimizing water use and recovering it for reuse, breweries can move towards water neutrality. This can eventually enable them to achieve water-positive operations,” says Maria.
The solutions are already available, with one that significantly contributes to water efficiency being the Alfa Laval Revos Concentration System.
As the name suggests, the solution uses reverse osmosis to make a beer concentrate and enable the recovery of food-grade water while preserving the full range of flavours, aromas, and other distinctive characteristics of the beer.
“The amount of water recovered from a beer during concentration with Revos depends on the beer. A 5-percent beer can be concentrated 4.4 times, which means that around 70 percent of water is recovered. This water is perfectly suitable for reuse upstream to make new beer, as an ingredient in other beverages, or hygienic cleaning-in-place,” she says.
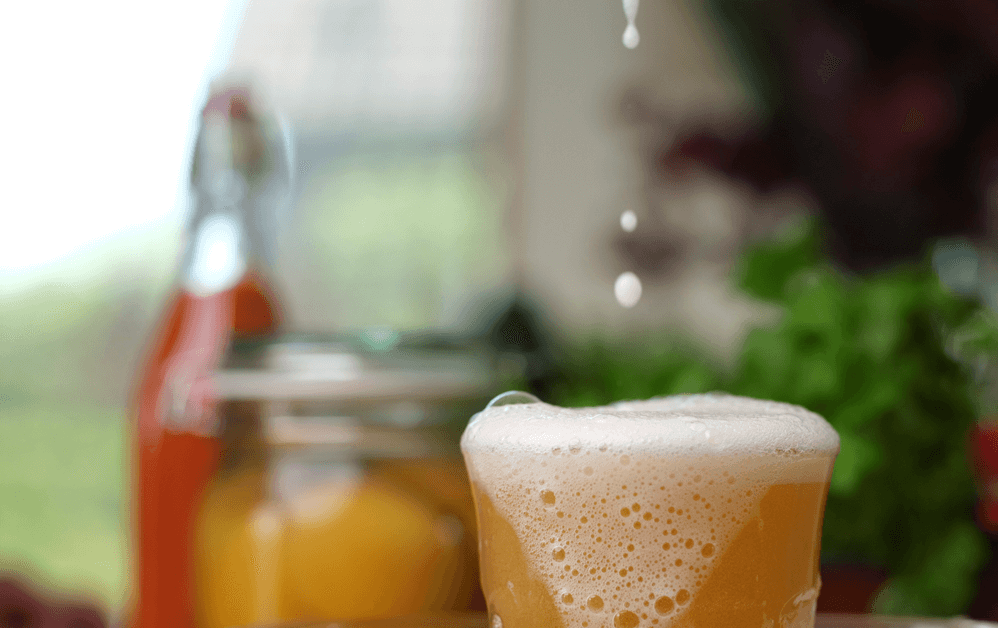
Supply chain
Conventional breweries frequently transport large volumes of beer across a continent from one country to another and even across continents. “In effect, large quantities of water are being removed from one local system and injected into another –with a considerable effect on the brewery’s scope-3 carbon footprint. This is not in line with sustainable practices. And it is also costly to move water,” says Maria.
By adopting the Revos Concentration solution, breweries can keep water in the place where it is needed for brewing new beer, while reducing the need for transportation and the related carbon emissions by as much as 80 percent.
“For many breweries, the change to their supply chain will be limited to sending fewer trucks and fewer kegs out on the roads. Often, a brewery already has a packaging facility in the place where the beer is released for retail sale. So, the financial and environmental gains from concentrating beer ahead of transportation and re-diluting it in the locale of consumption are substantial,” says Maria.
In fact, with the Revos Concentration solution, a brewery can optimize their supply chain even further, says Maria. “Kegs with concentrated beer can be re-diluted using the Alfa Laval Re-draft solution. In this way, the concentrated beer can be dispensed at a pub or restaurant just before being served to a thirsty customer.”
New interest
Maria has observed new interest in the Revos concentration solution from breweries in Mediterranean countries after unusually extreme weather conditions during the summer of 2023 forced many municipalities to restrict industrial water withdrawals by up to 20 percent. This had a direct impact on the amount of beer sold.
“Initially, it may be the profitability gain of the Revos solution that attracts breweries’ attention to this solution – until they discover the positive impact on their water consumption. For obvious reasons, water preservation must happen locally in the place where the brewery needs the water and ultimately where the beer is consumed. And this is what Revos enables. It is an attractive solution for breweries in need of strengthening the circular use of water as part of a larger process to optimize their water footprint and build resilience to disruption of local water supplies,” says Maria.
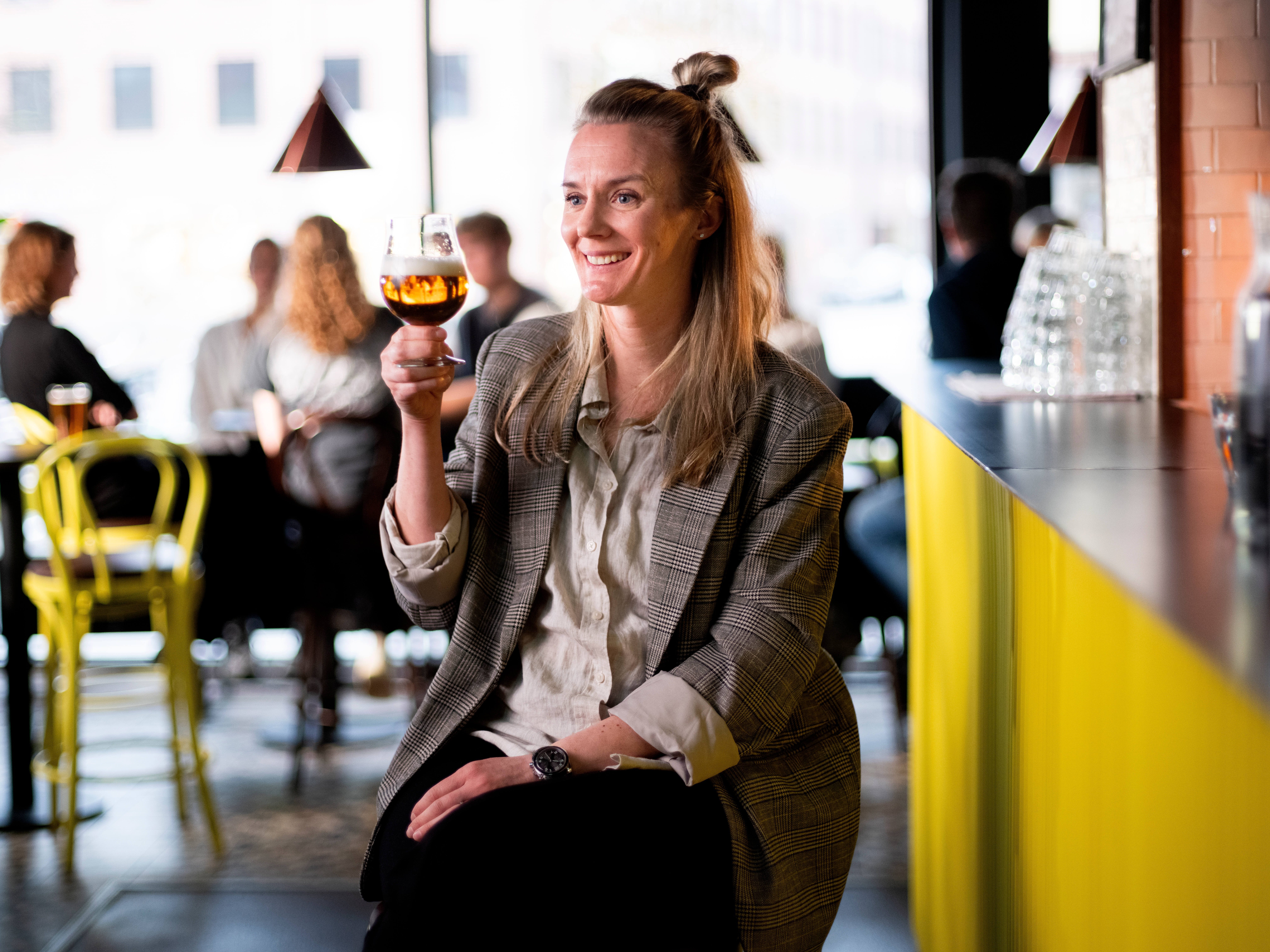
Maria Lindmark has over 10 years’ experience as a business development director. During this time, she has worked with the commercial side of beer in an international context and can count Carlsberg to the list of former employers on her resume.
In her current position, she leads business development of the Alfa Laval Revos beer concentration solution; the company’s most innovative technology offering for breweries.
She is passionate about bringing beer to the right destination in the most cost-effective and environmentally friendly way, without compromising the consumer experience.
Water savings
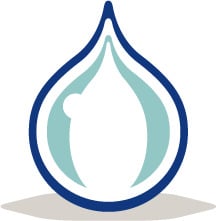
A 5-percent beer can be concentrated 4.4 times, which means that around 70 percent of water is recovered.
CO2 savings
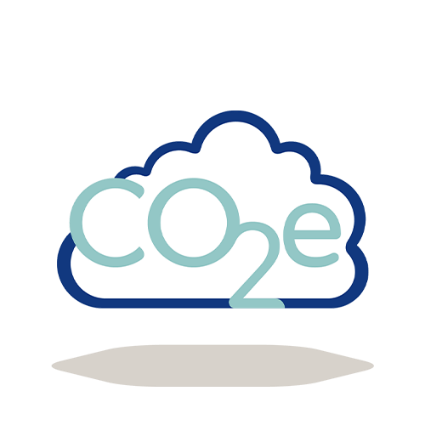
The Revos Concentration solution will reduce the number of trucks for transportation and the corresponding CO2-e emissions by up to 80 percent.
Recovered permeate
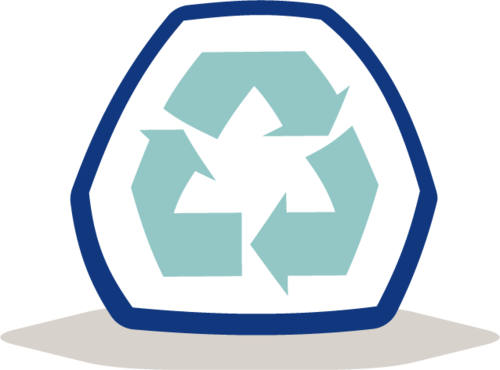
The recovered permeate is food-grade water and can be freely used for producing new beer, as an ingredient for other beverages, or for cleaning-in-place.