Energy saving adds 2000 EUR/day to ethanol producer’s bottom line
At a large ethanol producer in Belgium, heat recovery and water reuse were high on the sustainability agenda, while the company also wanted to improve its profitability and competitiveness.
DATE 2023-11-28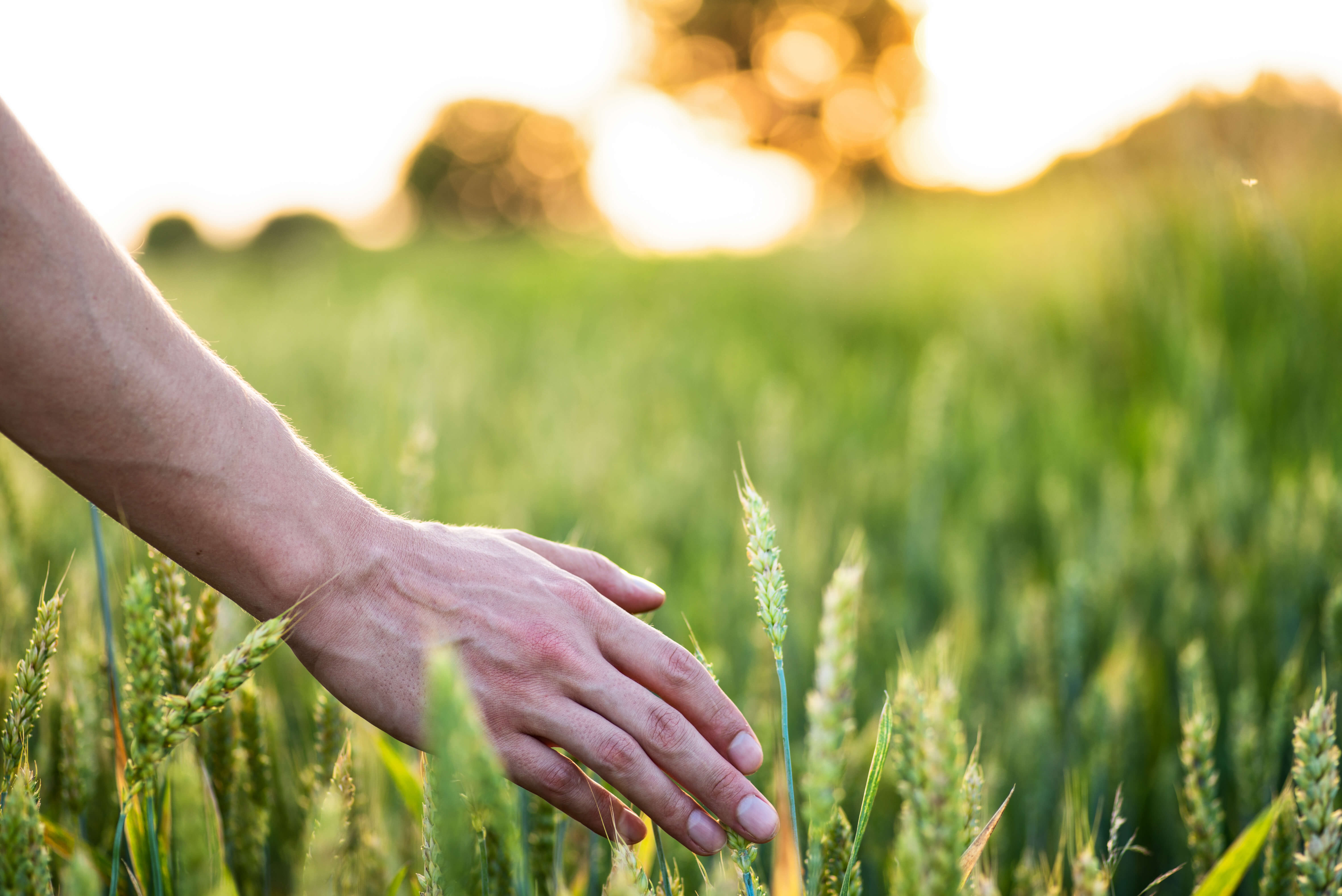
The customer was working with a US system integrator, who brought in Alfa Laval for its expertise with WideGap gasketed plate heat exchangers, which were key to meeting the sustainability targets.
The heat exchangers have increased the energy efficiency of the plant’s mash cooling line by 4000kWh, with the resulting energy recovered corresponding to a saving of 2000EUR/day.
The solution incorporates two new WG350X wide gap gasketed plate heat exchangers into the mash cooling line – one in operation and one on stand-by – and utilizes water from the downstream distillation process.
Using this process water to cool the mash from 90ºC to around 60ºC generates hot water, which can then be re-used upstream to save energy.
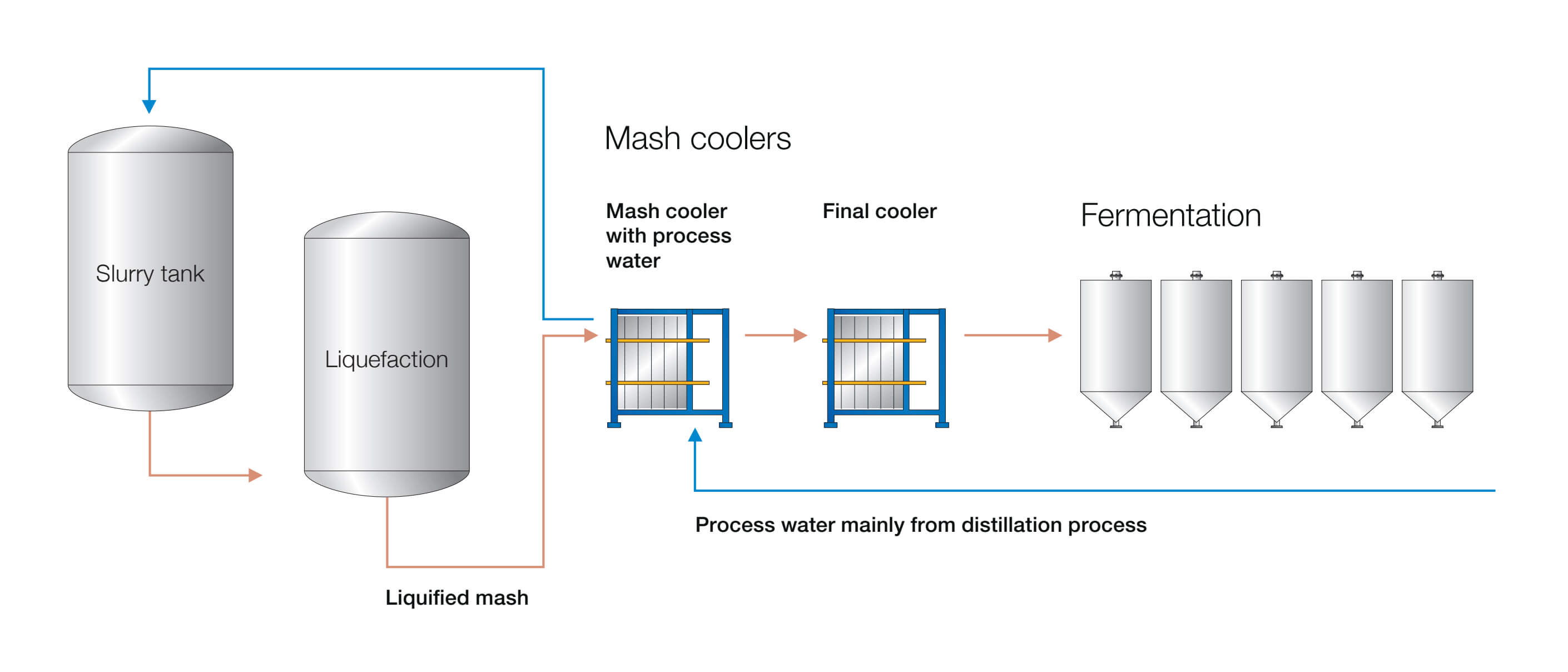
“Our experience in this application enabled us to design the unit in an optimal way for the customer,” explains Senior Global Technology Application Process Engineer Eser Aydin. “In this corn-based ethanol process, the stream is a slurry containing suspended particles and corn fibre. Our WideGap heat exchanger can handle this duty more efficiently with a tighter temperature approach and longer intervals between cleaning. Additional support with a recommended maintenance programme to optimize performance maximized the plant’s profit.”
Payback on investment is six months, and the potential added value in terms of sustainability and reduced carbon emissions, together with the Opex savings over the lifetime of the equipment, were an attractive proposition for this customer in the highly competitive ethanol market.
“We offered a different solution, and the customer liked this approach,” concludes Eser. “Going forward, we can demonstrate that it will pay off for customers to invest in an audit and potential redesign of their existing installed unit according to the current operational conditions so that instead of just designing for the required duty, we will focus on energy-efficiency in our discussions with customers and how optimizing a process has the potential to save energy and ultimately costs in their operation.”
Highlighted Technologies
Energy savings
Energy saving of 4000kWh with the resulting energy recovered corresponding to a saving of 2000EUR/day.
Payback time
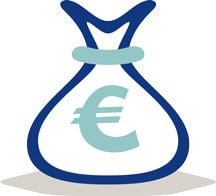
The payback time is 6 months.
CO2
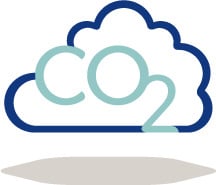
5000 tonnes/year.