Creating a path to energy efficiency with the Aalborg Micro economizer
DFDS is one of the busiest shipping companies in Northern Europe, operating freight and passenger vessels on the North Sea, Baltic Sea and English Channel. For more than 50 years, the company has relied on Alfa Laval in diverse applications. One is waste heat recovery, where the Alfa Laval Aalborg Micro economizer gave three DFDS ferries a once unthinkable solution.
DATE 2023-11-28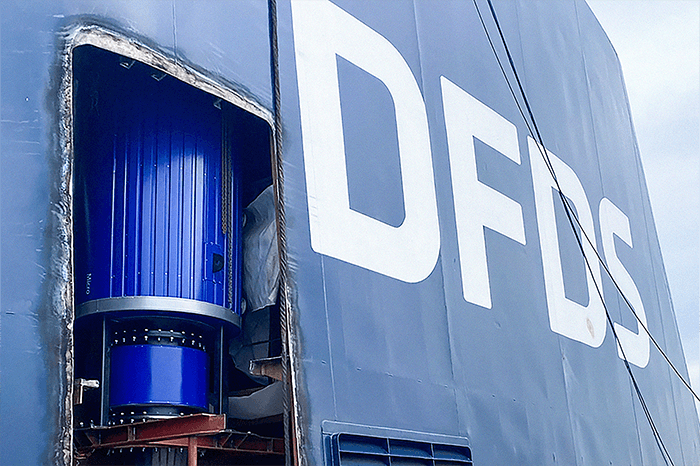
Ferries with no waste heat recovery
DFDS has three ferries on its English Channel route between Dover and Dunkirk. These were purchased from another shipowner who had built them around 15 years ago. Unfortunately, they were designed without any waste heat recovery systems – presumably due to the space taken up by the exhaust gas boilers available at the time.
“Normally, in the ferry and RoRo business we operate in, you would always include waste heat recovery systems,” says Jan Blak, Superintendent at DFDS. “Here, we’ve had to supply all the steam needed with the two oil-fired boilers on board. Ferries consume a substantial amount of steam for industrial purposes, but there’s also a significant consumption for domestic needs, such as heating the accommodation.”
No conventional solution
Producing all steam by burning fuel oil was a source of frustration for DFDS, especially given the growing focus on emissions and energy efficiency. In 2012, the company conducted a feasibility study for the retrofit of waste heat recovery. Unfortunately, it proved impossible to achieve full coverage – even with a major rebuild.
“It would have meant sacrificing car deck just to extend the funnel casing, plus a lot of equipment relocation,” Blak explains. “There was just no way to fit conventional exhaust gas boilers on all four main engines. In the best case, we could have extracted the heat from two. But these vessels can operate with two, three or four main engines running, and the configuration varies. At times we would have been running without waste heat recovery connected, so we had to abandon the idea.”
Then, a year and a half ago, everything changed for Blak and his colleagues: “We began investigating after seeing the new Aalborg Micro economizer, and we found a solution that is way, way better.”
New possibilities with 100% coverage
With its unique flexibility, the Aalborg Micro finally opened the door to waste heat recovery on the DFDS ferries. Besides fitting in without claiming cargo space, it was able cover all operating scenarios.
“We came up with a solution where each of the four main engines has its own Aalborg Micro, all of which feed into a common steam drum,” says Blak. “No matter which engine configuration is running, waste heat can always be extracted. Sometimes there will even be surplus steam, like in the worst-case scenario when all engines are running, so there’s also a dump condenser.”
In fact, there was even room for an additional Aalborg Micro to serve the genset on board. This was an added plus, since no shore power is currently available in Dover or Dunkirk.
“When we’re in port, we can still cover some of our steam consumption using the Micro on the generator,” Blak says. “It wouldn’t have made sense to not include the generator in this.”
Retained cargo space and stability
DFDS moved quickly on the Aalborg Micro solution, installing it on all three ferries in early 2022. Everything – from the economizers themselves to the shared steam drum and circulation pumps – was slipped into unused space within the funnel casing, where steel support structures and maintenance access had been added. The main engine economizers were lowered through a hole cut in the funnel top plate, while the genset economizer was lifted into a separate compartment through the funnel’s side. By the third installation, the process had been streamlined to just 18 days.
“In fact, we installed the Aalborg Micros in the upper part of the funnel casing, which is absolutely the worst place to put additional weight on a ship,” Blak remarks. “But because the Micros are so light, we’ve stayed within the stability requirements. There’s no loss of cargo and no major impact on stability, which is really amazing.”
The game-changing Aalborg Micro
The Aalborg Micro is an alternative to conventional exhaust gas boilers, offering higher efficiency and a radically reduced footprint. Designed to utilize an external steam space, for example by sharing the steam drum of a connected oil-fired boiler, it has no steam space of its own. This makes it small and extremely light.
“The water in a conventional exhaust gas boiler adds many tonnes of dead weight,” says Blak.
“In an Aalborg Micro, you have only around 200 kilos of water, because it’s basically a thin heating coil inside an empty shell. That makes the Micro very, very light and compact compared to conventional systems, which is absolutely the biggest advantage.”
Jan Blak, Superintendent at DFDS
Better fuel economy, lower vessel emissions
The Aalborg Micro solution has been operating for a few months, and tuning is still underway. Yet the results on the ferries are already promising. Current figures show the amount of fuel consumed by the oil-fired boilers is down by 70–80%. At that rate of savings and at current fuel prices, the investment will pay itself back within just a few years.
Blak points out that the monetary and environmental benefits are difficult to separate.
“As soon as we start saving fuel, we start saving money but also minimize our emissions,” Blak explains. “Compared to many other emission-reducing initiatives, the Aalborg Micro has a really good business case. We save from day one, so it’s a win-win any way you look at it.”
Tags
All