Cooling naturally
A new district cooling plant uses seawater and natural refrigerants to supply cooling to nearby stores and offices in central Copenhagen. With district cooling the buildings can do away with huge air-conditioning systems, thus saving space, energy and CO2 emissions.
DATE 2023-11-28 AUTHOR Jack JacksonIn central Copenhagen, the red-brick smokestack on Gothersgade street used to send black smoke into the skies of this old, scenic part of the city, which is situated only a few blocks from the wooden ships, castles and sidewalk cafes of Kongens Nytorv. Since it shut down in the 1970s, Copenhagen’s oldest power plant has stood vacant. Today the plant runs again. It is smoke-free and does not generate electricity but rather something else entirely, saving its customers 7 GWh of power and 3,000 tonnes of CO2 emissions a year. Using the old, underground district heating network, the Gothersgade Works now provides district cooling.
The facility, owned by Copenhagen power utility Copenhagen Energy, supplies cooling to nearby banks, department stores and offices, keeping their computer server rooms and other areas cool and comfortable year-round. The plant runs with the help of natural refrigerants and local resources such as seawater and waste heat, keeping costs down and environmental benefits up.
District cooling works on the same basic principle as district heating, but with cold rather than hot water: A central plant produces chilled water and distributes it through an underground network of insulated pipes. Customers that connect to the pipeline network can use the amount of the chilled water required to fulfil their own cooling needs. Calculations show that customers changing over to district cooling can reduce their operational costs by up to 45 percent, including huge savings on electricity and expenses for service and repair.
Installation costs for district cooling are also much less than for individual cooling systems. All that is needed is a special heat exchanger unit and pump for customers to chill their own central cooling system water. They can then dispose of their conventional chilling units, opening up space and cutting electricity consumption for cooling, says Jan Don Høgh, department manager of Copenhagen Energy. “It depends upon how efficient a customer’s cooling system is, but so far we have seen cost savings of 10 to 55 percent,” Høgh says. “Usually a building’s [individual] central cooling system will need motors, pumps, filters, condensers and towers, and it might take up 300 square metres,” Høgh says. “A district cooling installation has no moving parts, meaning it doesn’t generate noise, and it uses three to four square metres.
That’s important in this part of the city, where space is extremely valuable.” One of Copenhagen Energy’s first customers, the Berlingske media house, added two extra employee parking spaces when it switched from its traditional air-conditioning system to district cooling, winning the space with the removal of gear in its garage. Even better, when the chilling components were dismantled from its roof, it could build a new cafeteria and conference rooms with a great view over the city.
District cooling also reduces emissions. According to calculations by Copenhagen Energy, comparing district cooling with energy consumption and emissions figures for individual cooling plants in the buildings on Kongens Nytorv, there is a 66 percent savings to be made in CO2 emissions per year. For sulphur dioxide (SO2) and nitrogen oxide (NOx), the annual savings is 62 percent and 69 percent, respectively.
The district cooling plant facility uses two 100-year-old cement pipelines that bring in seawater from 800 metres away – the essential factor in the plant’s economic and environmental accounting. When the seawater is cold enough (from November to April), it does all the chilling work alone in a free cooling unit (see box on page 12). The rest of the year, the seawater is used as a cooling agent in the condensers of compressor chillers that use ammonia as a natural refrigerant.
In the summer, during times when cooling demand is highest, the plant also uses an absorption chiller that runs on waste steam from a local waste incineration plant, a process that’s termed “absorption cooling”. “If you consider this excess heat as pure waste, then the absorption chiller is almost 100 percent CO2-neutral,” says Høgh during a tour of the facility. He has to yell to be heard over the hum and buzz of the pumps and machinery, with its maze of thick silver tubes for the flowing cold water.
Copenhagen Energy’s 12 MW plant started production in March 2010. While it was under construction in December 2009, several delegations from the UN-COP15 climate conference in Copenhagen came by for a tour to observe how it would be possible to reduce energy consumption for cooling in energy-demanding buildings. Just recently another of many Chinese groups visited. “They’re very interested in district cooling,” Høgh says. “They see it as a super alternative to what they have in their cities today.”
The demand for cooling has been constantly increasing over the past 10 years, partly due to the growing use of IT and data storage. According to Copenhagen Energy, 40 to 50 percent of its customers’ cooling demand is actually used in their server rooms. The district cooling technology works anywhere, but it is competitive only with certain key conditions, says Keld Almegaard of COWI, the engineering consultant who helped make the Copenhagen plant possible. “It has to be sized for at least 10 MW, and it’s a good idea to have a harbour or source of water nearby – as well as access to waste heat,” says Almegaard.
Copenhagen Energy had been ready for some time to start up the district cooling plant, but it wasn’t until 2009 that the Danish legislative framework made it possible to operate district cooling systems. “We saw a huge potential for this in Denmark,” Høgh says. One more facility is in the pipeline for Copenhagen, with six other possible sites in planning. District cooling already had up to 15 years of success in a few European cities – with 450 MW of capacity in Stockholm and 550 MW in Paris – and, says Høgh, new projects are in the pipeline around the continent.
District cooling also provides a simple and economical way for building owners to phase out their chilling systems that run on hydrofluorocarbons or other synthetic fluorinated f-gases. These are the devastating greenhouse gases under scrutiny from the United Nations, environmental advocates and consumer groups (see story on page 6). Denmark requires a total phase-out by 2015.
“We’re purely customer driven,” says Høgh. “This is a competitive concept where we can reduce CO2 emissions without any subsidies. It won’t solve all the challenges Denmark has to reduce its greenhouse gas emissions, but it’s one step to getting there.”
Solutions with natural refrigerants readily available
Alfa Laval’s solutions enable a shift away from harmful refrigerants to three common, environmentally friendly natural refrigerants: carbon dioxide, ammonia and hydrocarbons.
Carbon dioxide (CO2): Supermarket refrigeration systems are increasingly using CO2 as a refrigerant, as well as for condensing or cooling gases at an ambient temperature. This solution works best in cooler climates, says Tommy Ångbäck, manager, Refrigeration & HVAC Cooling at Alfa Laval. Several Scandinavian and UK supermarket chains now use CO2 as a standard solution. CO2’s physical properties require refrigeration systems to operate at more than five times the normal pressure of a classic refrigeration system.
This puts new challenges on the components in the system. Alfa Laval has developed a full range of heat exchangers to cope efficiently with these high-pressure systems. The range of heat exchangers for CO2 applications includes cold room air coolers and ambient air gas coolers, along with brazed plate heat exchangers used as CO2 economizers, evaporators or heat recovery gas coolers.
Ammonia: A modern ammonia refrigeration system offers good payback over the longer term, according to Ångbäck. Today’s plate heat exchangers can reduce the volume of ammonia by 10 times or more on bigger indirect refrigeration systems compared with the old-fashioned shell-and-tube ammonia systems.
“We’ve supplied thousands of compact, efficient solutions with semi-welded plate heat exchangers with welded cassettes for large ammonia refrigeration plants,” Ångbäck says. “These can now also handle higher pressures to deal with ammonia/CO2 two-stage cascade systems for increased energy performance in low-temperature applications.” Smaller systems can apply the AlfaNova fusion-brazed plate heat exchangers made of 100 percent stainless steel. “You only need a very low charge of ammonia, and this makes the system cheaper and safer,” says Ångbäck.
Hydrocarbons: Hydrocarbons are now widely used in household refrigeration appliances to replace harmful refrigerants. Bigger commercial systems can also run with propane as the refrigerant. Alfa Laval’s copper-brazed plate heat exchangers then come in handy to keep the flammable propane gas volume as low as possible in an indirect system, typically using a glycol solution or liquid CO2 as a secondary coolant, says Ångbäck.
Smart system leads to efficient cooling
Copenhagen Energy’s district cooling plant has a capacity of about 12 MW and is based on three different principles of cooling – free cooling, absorption cooling and compressor-based cooling. This makes it a very flexible and highly energy-efficient system.
Alfa Laval has delivered seven plate heat exchangers to the plant: one titanium plate heat exchanger, three evaporators and three condensers. Copenhagen Energy’s Jan Don Høgh says the reasons for choosing Alfa Laval’s heat exchangers are their “high efficiency and low pressure losses.” Besides, he says, “Alfa Laval is a well-known supplier of heat exchangers.” The Alfa Laval titanium plate heat exchanger is used in the free cooling system where seawater is pumped up from the Port of Copenhagen and used to cool the district cooling water. Titanium plates must be used to avoid corrosion from the saltwater. In winter, when the seawater temperature is below 5.5°C and cooling demand is less than 2400 kW,
Copenhagen Energy uses the free cooling system alone to cool the district cooling water. When the seawater temperature is between 5.5°C and 11.5°C, the heat exchanger is used for precooling of the cooled water, before it’s cooled by a compressor chiller system to the desired temperature. The Copenhagen plant has three such chiller systems. Each incorporates one Alfa Laval stainless steel evaporator and one Alfa Laval titanium condenser.
The seawater is then used to cool the natural refrigerant ammonia in the condensers. When the seawater temperature is above 11.5°C, the seawater is too warm to be used for free cooling, and the chillers provide all cooling.
The free cooling system is highly energy-efficient, explains Alireza Rasti, sales manager, Alfa Laval in Denmark. “When the seawater is cold enough to do the cooling job by itself, you don’t have to run the compressors,” he says. “By running only the seawater pumps, you consume only a fraction of the electricity usually needed.”
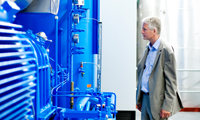
Customer's voice
We’re purely customer driven. This is a competitive concept where we can reduce CO2 emissions without any subsidies.
Jan don Hogh, Copenhagen Energy