Saving space, with cool results
When F.X. Matt brewing Co., one of the oldest family owned breweries and the 15th largest beer producer in the US needed a space-saving system Alfa Laval came up with a compact solution with optimal energy-efficiency.
DATE 2023-11-28The challenge
Matt Brewing Co., based in Utica, NY has been brewing beer and soda since 1888. Each year, the brewery produces more than 65 varieties/recipes, using its signature copper boiling kettles. The brewery needed a refrigeration system for its Saranac brand of beer,
The solution
With the brewery's cooling needs and confined space in mind, Alfa Laval proposed two compact refrigeration systems that would fit in the existing space – one consisting of an Alfa Laval M10 Semi-welded plate heat exchanger with a U-Turn plug-and-play liquid separator, and the second, an Alfa Laval M15 Semi-welded plate heat exchanger, also with a U-Turn. The first system would be used to cool beer when the process load was under capacity, while the second would be brought online when capacity was at full demand.
In addition to their compact design, the semi-welded plate heat exchangers allow for closer refrigerant to beer approach temperature than shell-and-tube heat exchangers, saving energy costs. This allows the brewery to reduce the temperature of the beer to 30°F (-1°C) with 26°F (-3°C) ammonia, instead of the 20°F (-7°C) ammonia a shell-and-tube heat exchanger would require.
The plate heat exchangers and U-Turn combination were delivered fully assembled. They were small enough to fit in the available space and didn't require additional structure support or piping. The only things required prior to startup were controls and refrigerant valves. This resulted in tremendous savings in design, installation and downtime costs for the company. Located above the plate heat exchangers, the curved shape of the U-Turn separators reduces the length of the unit by half, resulting in an extremely small installation footprint.
In addition to conventional gravitational separation, the unique U-Turn module utilizes agglomeration, surface tension and centrifugal forces to reduce the refrigerant charge. The low pressure drop - up to four times lower than a conventional system - makes it more energy-efficient and reduces the required refrigerant charge. This also helps keep the brewery operating below EPA restrictions, thus minimizing environmental impact. Furthermore, the compact design makes it easy to connect the module to an existing cooling system.
The result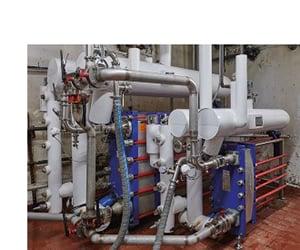
The U-Turn systems now produce beer at output temperatures below anything the brewery has ever achieved, 30°F (-1°C) compared to 33°F (1°C), allowing for higher production yields. An ideal solution, the brewery saved considerable costs on construction, design, and materials – and will continue to save on energy costs.
Download the full story
A U-Turn installed with a semi-welded heat exchanger.
Saranac's two new refrigerant systems to cool beer.
- Alfa Laval M10-BW Semi-welded plate heat exchanger and U-Turn plug-and-play module cools beer from 60°F (16°C) to 30°F (-1°C) at 120 gpm for a load around 150 TR (527.5kW).
- Alfa Laval MK15-BW Semi-welded plate heat exchanger and U-Turn separator cools beer from 60°F (16°C) to 30°F (-1°C) at 250 gpm for a load around 300 TR (1055kW).
Why the customer chose Alfa Laval
- By choosing the semi-welded technology the footprint demanded three times less space than an expansion of the existing shell-and-tube solution have required.
- Low refrigerant charge design of the U-Turn and plate heat exchanger - only a third of a conventional system.
- Cost savings - construction, design, materials
- Improved efficiency of the cooling system - reduced energy consumption.