Non-alcoholic brewing – new technologies and big opportunities
Tastes are changing – new thinking needed
DATE 2023-11-28The world has enjoyed non-alcoholic or low-alcohol beer for the past 30 years. But recently quality 0.0 beers have gained wider consumer acceptance and broad success. Which is why beer dealcoholization—stripping alcohol from dedicated final beer recipes to less than 0.05% ABV—is taking off in a big way.
Health- and taste-conscious consumers are increasingly now choosing low- and no-alcohol beer to socialize, drink responsibly and save lives. To meet growing demand, traditional brewers must adapt process lines—without compromising flavour, aroma or mouthfeel. This requires a deep understanding of the processes, equipment and systems in place and how best to optimize these to capitalize on the opportunities that 0.0 beer presents.
Embrace 0.0 beer with confidence. Get the process know-how and technical support you need from Alfa Laval. Then enjoy higher profits, lower taxes and new surplus alcohol revenue streams that add value to your brewery business.
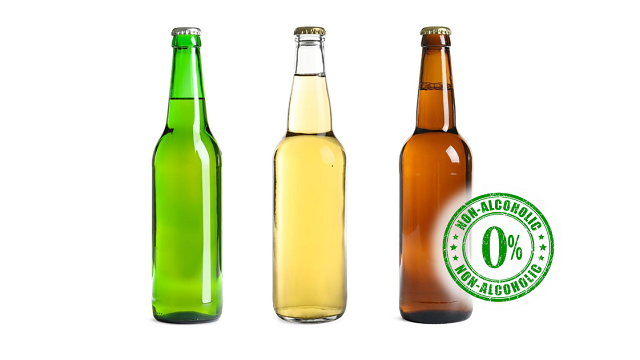
Removing alcohol from beer
There’s no way around it. Brewing zero-alcohol beer requires wort mashing and boiling to hops blending and fermentation, which produces ethanol. How best do you remove alcohol from beer? By using an appropriate stripping or filtration technology. What you get is an alcohol concentrate, though its strength will vary. To separate the alcohol (ethanol condensate), you can take one of these three approaches without having to add explosion-proof (ATEX) zones to your brewery process lines:
1. Diluting and draining
You can reuse seal water from vacuum pump seals to dilute a condensate with approximately 18-35% alcohol by volume, depending on incoming beer alcohol content. Diluting the ethanol this way ensures that the fluid will always be below the flash point and, as a result, not require any ATEX zone. The diluted ethanol can then be drained or collected, which is common practice if there is no other application or use for it.
2. Adding value to beer products
Produce new high-value beer by adding this clear food-grade neutral alcohol condensate (18-35% ABV) as an ingredient to other beer products. Topping up the alcohol strength of your existing range of products adds value and opens up new revenue streams while enhancing beer flavour.
3. Creating new high-value beverages
Another option: Using the clear food-grade neutral alcohol condensate as an ingredient for new high-value products such as ready-to-drink cocktails, flavoured beer-based drinks, and even new hybrid products such as beer cocktails using vodka or barley-based alcohol products. Here surplus alcohol adds value by enhancing the flavour, a perk much appreciated by beer lovers.
How low can you go?
Going from 4.5% alcohol content to 0.5 to 0.0 takes know-how. Especially if you want to preserve all the characteristics that people want from a good brew—aroma, flavour, mouthfeel and more. To shift gears from high to low alcohol content, you need a partner who understands how to manage yeast cultures, how malt types and fermentation techniques affect your brew, and how best to adjust flavour and aroma downstream after removing the alcohol. With vast brewery expertise, craftsmanship, technology and marketing skills, Alfa Laval may just be the right partner for you.
Brew great-tasting zero-alcohol beer
It’s easy—with the Alfa Laval Dealcoholization Module. This specially designed, all-in-one module combines proven technologies—from beer degassing and culinary steam generation to vacuum stripping and alcohol condensing—to strip alcohol from beer, reliably and cost-effectively. Simply integrate your systems with this single-pass stripping column at low temperatures and pressures. No hassle. No major capital investments. Just great-tasting 0.0 beer. No kidding.
Plus discover new ways to get the most out of the ethanol stripped from your brew—like blending it to produce innovative alcoholic hybrids.