Packinox in hydrodesulfurization (HDS)
Alfa Laval Packinox is the perfect feed-effluent heat exchanger for middle-distillates hydrodesulfurization units, offering exceptional heat recovery and minimal pressure drop, all in a highly compact format. Replacing an existing shell-and-tube heat exchanger train with a single Packinox makes it possible to save 80-100% of the fuel gas consumption in the furnace and reduce CO2 emissions correspondingly. It also allows you to expand production capacity without upgrading any other equipment.
Maximize efficiency in HDS processes
- Reduce energy consumption by up to 100% in the preheater furnace thanks to Packinox’s exceptional heat transfer efficiency.
- Save up to 20,000 tonnes of CO2 emissions per year in a standard 50,000 bpsd unit.
- Expand production capacity without having to upgrade your furnace, reactor, cooling system, or compressor.
- The PlateWash system removes any fouling as soon as it starts to accumulate, all while the plant is in operation. No need for cleaning stops.
- Packinox heat exchangers have delivered reliable operation in HDS plants all over the world for more than 20 years.
Optimized for energy savings
Replacing the shell-and-tube heat exchanger train in your HDS process with a single Packinox feed/effluent heat exchanger results in a very large increase in energy recovery. With a hot approach temperature (HAT) as low as 5°C (9°F), compared to 30°C (54°F) for a shell-and-tube solution, a Packinox lets you reduce fuel gas consumption in the preheater furnace by roughly 80% – with a corresponding decrease in CO2 emissions. In case your process is exothermal, the saving can be up to 100%, meaning fuel gas firing is no longer required.
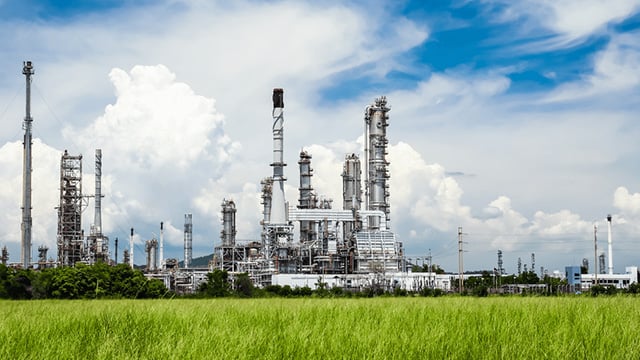
Integrated plate cleaning system
Alfa Laval PlateWash is a unique, integrated plate cleaning system for Packinox, specifically developed for low-temperature HDS processes where fouling often is a problem. The PlateWash system monitors the pressure drop in the heat exchanger and allows operators to engage water cleaning whenever ammonium salt fouling begins to accumulate. After a few hours of washing, the plates are clean again and the water spray is turned off. The washing process is performed during operation to maximize thermal efficiency over time and to avoid costly, unplanned downtime for cleaning.
The easy way to expand production capacity
Exchanging a shell-and-tube heat exchanger train for a single Packinox is the most cost-efficient way to expand production capacity in your HDS plant. Apart from a new heat exchanger, you do not need to make any additional equipment investments. The outstanding heat recovery adds both heating and cooling capacity to the process, meaning you can continue using your existing furnace and air-cooling system. In addition, the low pressure drop in a Packinox ensures you can continue using the same compressor too.
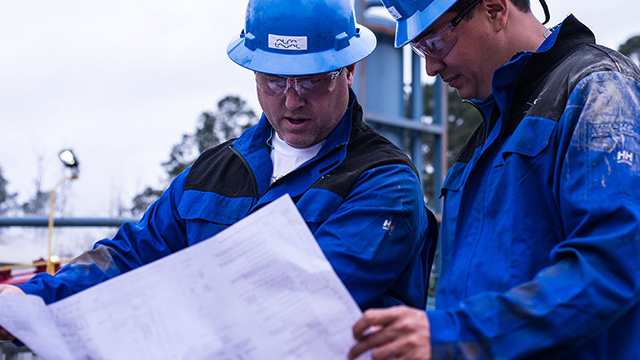
More than 20 years’ experience in HDS
Alfa Laval Packinox is mainly known for being the industry standard feed/effluent heat exchanger in catalytic reforming and aromatics plants. But we have also supplied high-efficiency heat exchangers for HDS applications for more than 20 years. Among the Packinox heat exchangers in operation in HDS plants around the world, the oldest has been in operation since July 2001 and is still delivering top performance. The diagram shows the HAT and pressure drop over time for a Packinox unit that has been in operation since 2011.
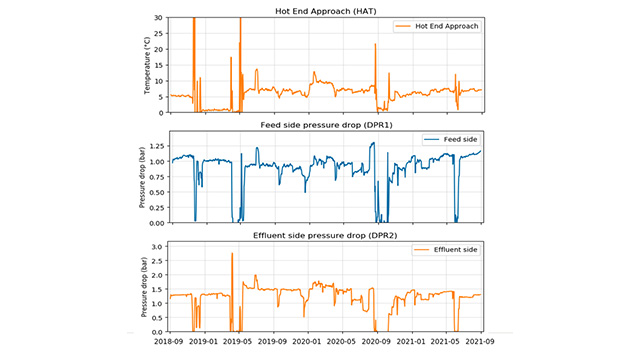
Discuss with an expert
Please contact one of our HDS application and Packinox experts, to discuss the opportunities in your HDS plant and how you can benefit from installing a Packinox feed/effluent heat exchanger.
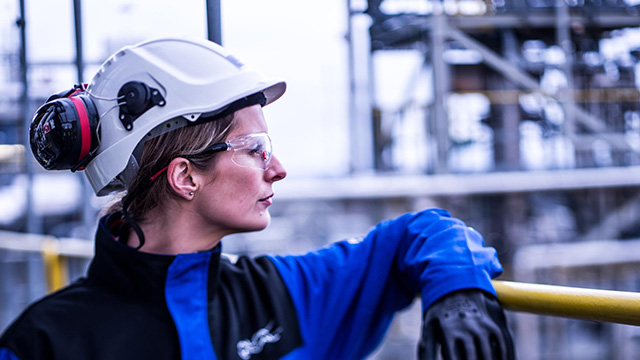
Packinox compared to shell-and-tube heat exchangers
Min. HAT | ΔP (both sides) | Cleaning during operation | Req. no. of units | Req. installation space | |
Packinox | 5°C (9°F) | 2 bar | Yes | 1 | Small |
Shell-and-tube HEX train | 30°C (54°F) | 4 bar | Yes | 4-5 | Large |
Solutions for catalytic hydrotreatment
Alfa Laval offers a range of products and solutions for catalytic hydrotreatment that help increase capacity, yield, and energy efficiency. Whether you are revamping an existing hydrotreater or adding a new process unit in your plant, Alfa Laval has the process knowhow to help you get the most out of your investment. Explore our products:
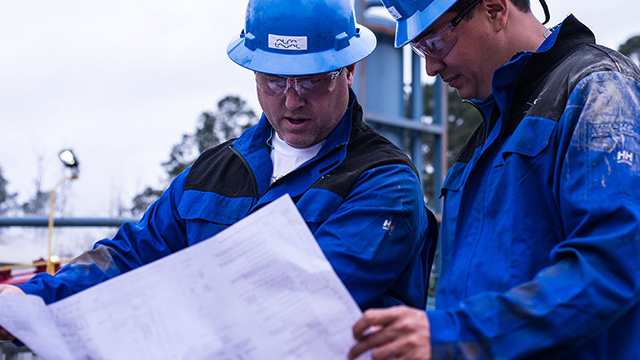
Documents
Documents
Product leaflets
Service from A to Z
Our team of service experts is ready to support you throughout the entire lifetime of your Packinox+ heat exchanger with every step from planning to execution.
We offer a complete range of on-site and remote services that ensure maximum operational reliability, great performance, and high total return on investment.
In this video you will see how we ensure performance over time.
Find out more about our service offerings for Packinox heat exchangers
Guaranteed performance
When investing in a Packinox heat exchanger you are not just buying a heat-transfer surface, you are investing in performance. Our unique performance guarantee gives you the peace of mind of knowing that your new heat exchanger will perform as specified.
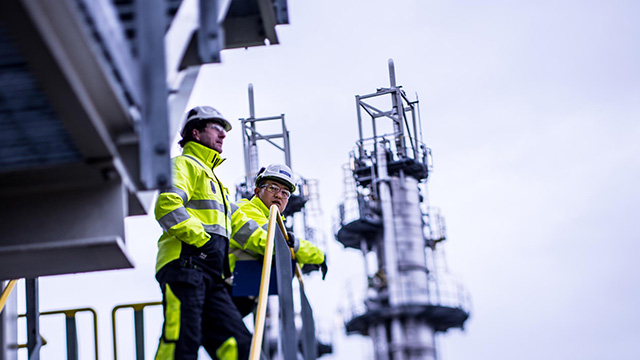
Fully customized
Every Packinox heat exchanger is tailored to the exact conditions that it will operate under. Choosing Packinox means you get a very accurate, optimized design, fine-tuned for maximum process yield and heat recovery. Our engineers cooperate closely with the world’s leading licensors and have more than 35 years’ experience of designing and manufacturing heat exchangers for the hydrocarbon industry. We make sure you get the best possible solution for your specific plant.
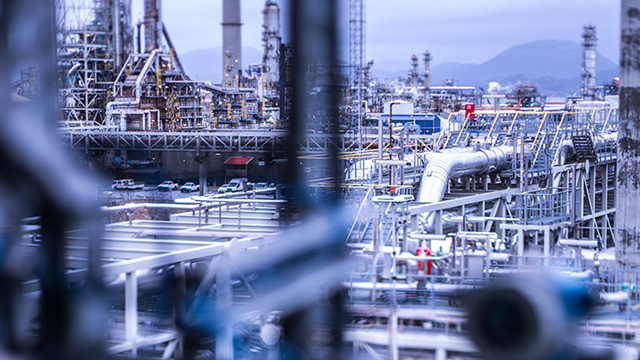
Built for maximum uptime
All welds subjected to high mechanical stress are laser welded for maximum strength and robustness. All welds are fully accessible for repairs, and individual channels can be plugged if necessary.
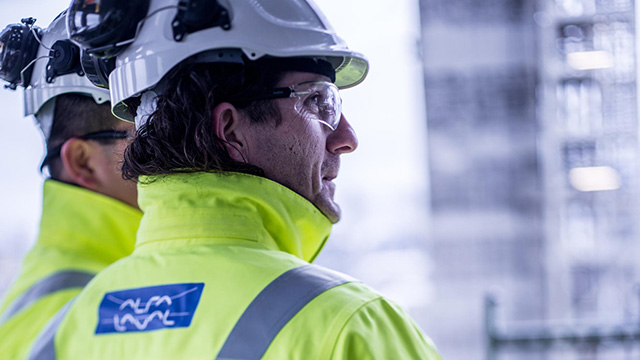
A high-efficiency solution for HDS
A Packinox heat exchanger combines high-pressure durability with superior thermal performance. The core of a Packinox heat exchanger is a fully welded pack of heat transfer plates where the hot and cold streams flow in alternate channels and in opposite directions. The counter-current flow maximizes heat transfer and makes it possible to operate with crossing temperatures in a single unit. The plate corrugation causes high turbulence in the media, resulting in maximum heat transfer and low fouling.
Replacing an entire shell-and-tube heat exchanger train
Thanks to its unique design, a Packinox offers outstanding performance in a compact unit. A single Packinox heat exchanger offers the same heat transfer capacity as multiple shell-and-tube heat exchangers with an equivalent heat transfer area of up to 35,000 m2.
Body flange
Optionally, the shell can be equipped with a body flange, allowing the entire top of the unit to be opened. This facilitates access to the plate pack greatly, enabling quick and easy upgrades.
Integrated cleaning system
For low-temperature HDS applications, where fouling is a problem, Packinox heat exchangers can be equipped with an integrated plate cleaning system called PlateWash. See the section above for more information.
High temperatures and pressures
The plate pack is positioned in a cylindrical pressure vessel, making it possible to operate at much higher pressures than traditional plate heat exchangers. The only limiting factors are the differential pressure between the two streams, which can be up to 70 bar, and the total design pressure of the pressure vessel. The maximum operating temperature is 500°C (930°F).
Unique features
The high thermal efficiency and operational reliability of a Packinox heat exchanger is the result of a number of innovations, including production methods, design solutions, and digital monitoring tools. Click the link below to learn more about how you can benefit from these unique features.