Introducing a new heat treatment technology for oat beverage
When a liquid food producer in northern Europe was looking to replace an existing heat exchanger which they used for heating up oat-base, they deviated from the conventional path by not choosing a shell & tube solution. Instead, they chose an HL8-WG from Alfa Laval’s Hygienic line. The new equipment was installed, and testing began in the autumn of 2019. Since then, the heat exchanger has been delivering a whole series of benefits, including minimized fouling, longer cleaning intervals, superior cleanability, and easier maintenance.
DATE 2024-03-19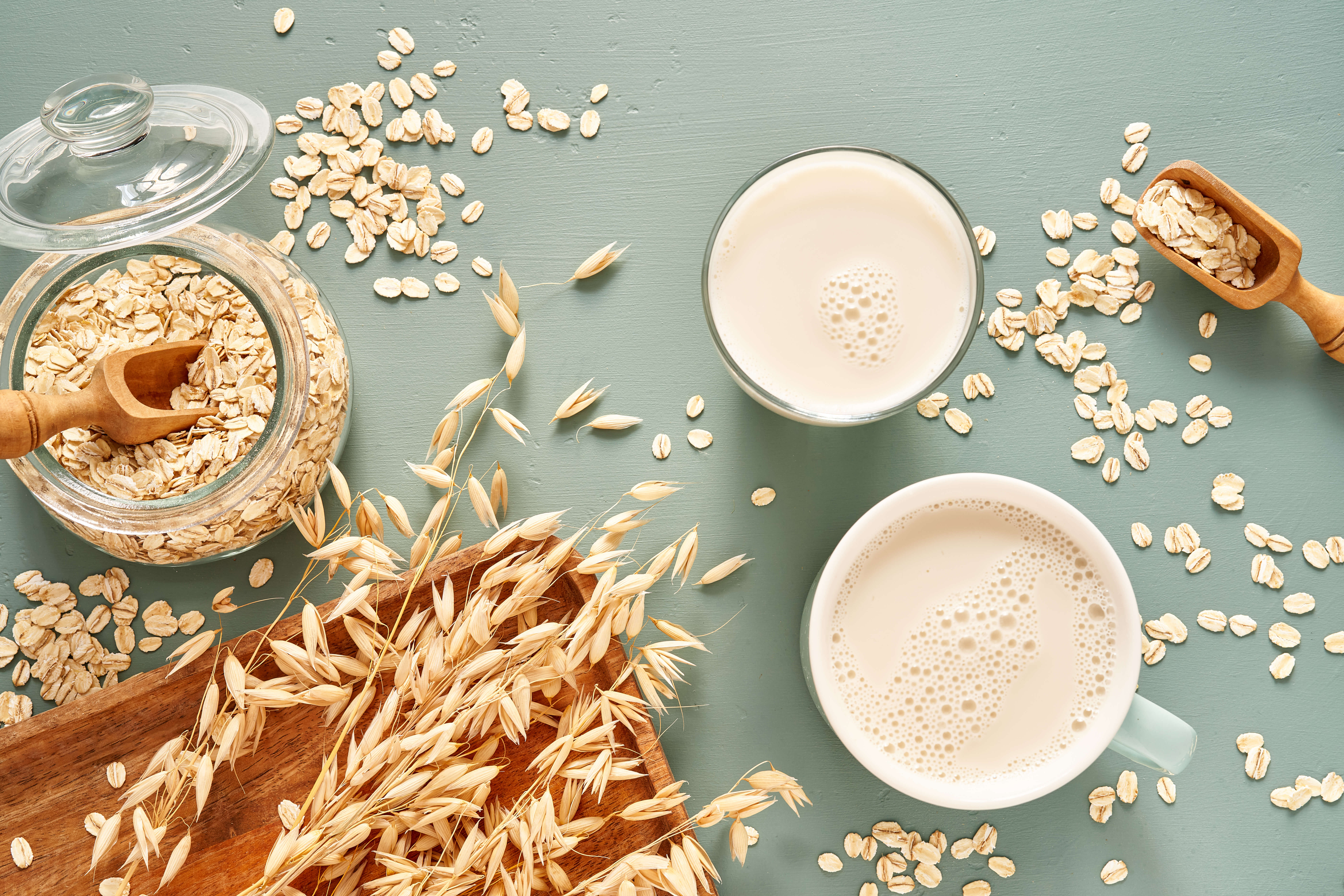
Choosing a new heat exchanger
The company in question was looking for a new type of heat exchanger to replace the hygienic plate heat exchanger they were using for the initial heating phase of their oat beverage production process.
Their main objective was to increase production capacity, which was, at the time, limited by the old heat exchanger’s need for frequent cleaning due to fouling build-up.
One alternative would have been to switch to a shell & tube solution, but they reasoned that this would mean longer heat treatment times, and there was a risk that it could affect the end product’s taste and texture.
After reviewing the options, they chose the HL8-WG from Alfa Laval – a hygienic WideGap plate heat exchanger that is more compact than a shell & tube and provides rapid heating to the correct temperature.
New design. New opportunities.
Alfa Laval’s Hygienic line of gasketed plate heat exchangers is designed specifically for products with the highest hygiene requirements. However, until recently, shell & tube technology was still the preferred solution for higher viscosity products with more and larger particles.
“The HL8-WG represents a new development step since it enables the use of gasketed plate heat exchangers in hygienic applications with particles and long fibres.” Says Alfa Laval Industrialization project manager Clemens Wictor, “Thanks to adjustments in the design, our hygienic WideGap heat exchangers can now be used in, e.g., plant-based drinks, juices with pulp and fibres, and fruit purées.”
Key design adjustments include the new OpenChannel™ plate pattern, which ensures long operating time with particles and fibres without clogging, and a feature called the SmoothPort™, which prevents build-up and maximizes both cleanability and drainability.
As a result of these developments, the HL8-WG requires less frequent cleaning and is easier to clean, reducing water consumption. Fouling build-up is minimized, leading to less of a pressure drop and a consequent reduction in energy consumption
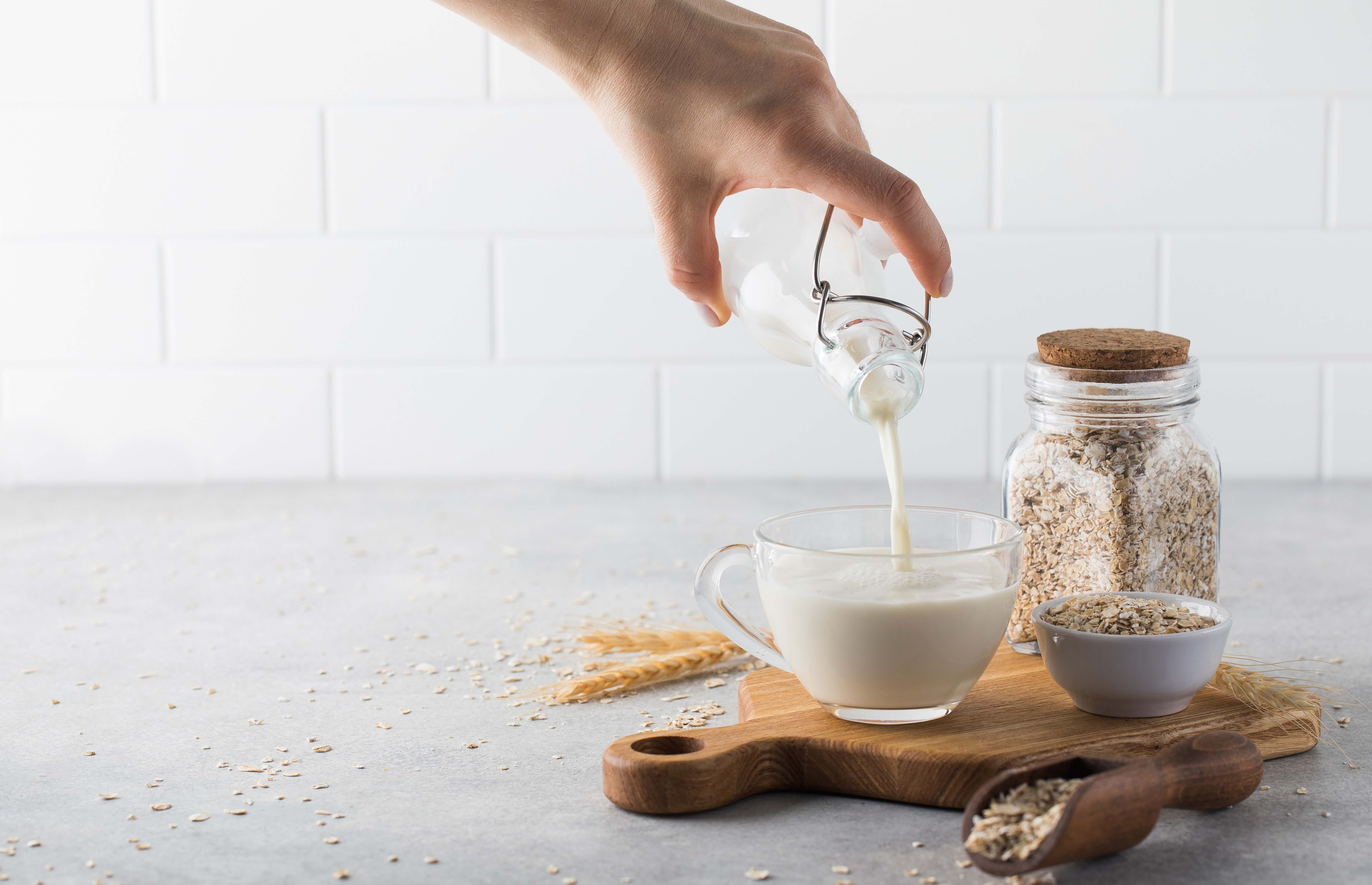
More flexibility for food producers
Before implementing the new HL8-WG at the customer’s plant, Alfa Laval’s test engineers ran comparative tests on a range of food applications where quality and hygiene are key. These included orange juice pulp, emulsion sauces with pickled vegetables and chunky tomato salsa. “The new heat exchanger outperformed shell & tube technology on all key parameters, including energy efficiency, material savings and process control”, says Clemens, “In all these tests, we could see that the HL8-WG gave better results. In fact, we’ve yet to find a challenge we can’t solve using our new hygienic WideGap heat exchanger technology. It gives food producers a whole new level of flexibility."
Longer production runs now possible
Our customer is now using the HL8-WG for the first stage of production where the oat mixture is still very fibrous. It enables longer production runs (18 to 20 hours), each of which is followed by a cleaning cycle, and no adjustments are required during production since the process remains stable with regard to, e.g., flow and temperature. After testing several different cleaning protocols, operators observed that no product residue remained between the gasket and the port. Previously, the heat exchanger had to be opened for mechanical cleaning at least once a month; now, it can run for periods of two months or longer without requiring mechanical cleaning.
The hunt for efficiency
The HL8-WG points to a future in which we can help food producers meet increasingly tough efficiency demands, specifically energy and water use. Compared with traditional plate heat exchangers, the HL8-WG requires less frequent cleaning, which saves CIP-water and increases productivity. Since the new heat exchangers don’t need to be opened as frequently, wear on the plates and gaskets is lower, and uptime is higher. Compared with traditional shell & tube heat exchangers, the HL8-WG is capable of a whole new level of heat recovery – up to 45% increase in heat recovery in some cases.
Highlighted Technologies
Water savings
Reduced cleaning chemical consumption
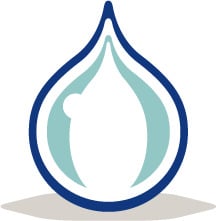
Water savings from extended cleaning intervals
Uptime
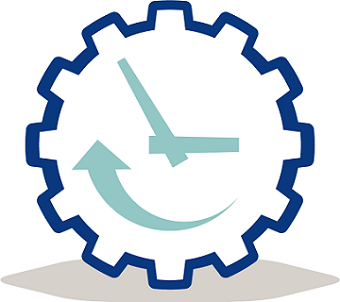
Increased uptime due to longer production runs
Sustainable food
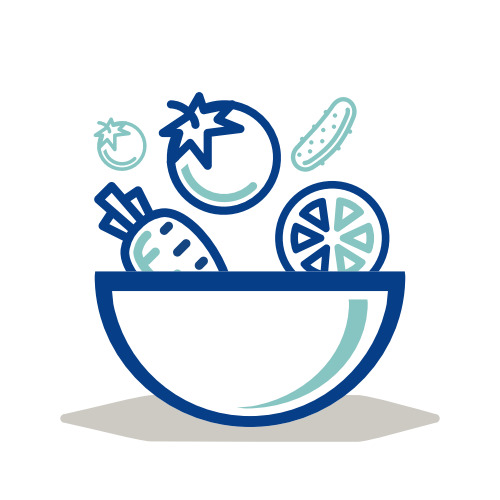
As a rule of thumb, the carbon footprint of plant-based foods is only half of that of animal-based equivalents
Why Alfa Laval HL8-WG?
- WideGap HEXs can require as little as 15% of the floor space needed for shell-and-tube heat exchangers (2 m2 vs. 13.5 m2 ). This also means transport and installation costs are lower.
- Their versatile design enables the capacity to be adjusted simply by adding or removing plates, all within the existing frame.
- Maintenance is easier since the heat transfer surfaces are easily accessible for inspection or mechanical cleaning.
- A specially designed plate pattern ensures a high degree of turbulence over the whole plate, which not only reduces fouling but also makes cleaning very effective.